Elite Electrical Contracting
Established in 1999, Elite Electrical Contracting Ltd. has built a solid reputation within the commercial fit-out sector, consistently delivering top-tier electrical services across a range of projects. Over more than two decades, the company has grown significantly under the guidance of its dedicated directors, culminating in a turnover exceeding £15 million annually. Elite Electrical’s success is anchored in its team of experienced professionals, whose commitment to excellence and innovation has made the company a recognised leader in its niche market.
The Critical Role of Advanced Electrical Installations
In today’s fast-paced manufacturing environment, the role of advanced electrical installations cannot be overstated. As industries evolve and the demand for efficiency, productivity, and sustainability intensifies, modern electrical systems have become the backbone of successful manufacturing operations. From powering sophisticated machinery to enabling smart technologies, electrical infrastructure plays a pivotal role in ensuring continuous, reliable production.
Impact on Manufacturing Efficiency and Sustainability
Advanced electrical installations are not just about providing power—they are integral to optimising processes, reducing downtime, and enhancing the overall sustainability of manufacturing operations. By integrating cutting-edge technologies such as automation, IoT, and energy management systems, manufacturers can significantly boost productivity while minimising environmental impact. As we explore the various facets of modern electrical installations, it becomes clear that these systems are crucial for manufacturers aiming to remain competitive in an increasingly challenging market.
The Role of Electrical Installations in Modern Manufacturing
Electrical installations form the foundation of modern manufacturing, ensuring that operations run smoothly and efficiently. In this section, we’ll explore how reliable electrical infrastructure supports continuous manufacturing, how Industry 4.0 technologies are transforming the landscape, and practical examples of these systems in action.
Foundational Importance: How Reliable Electrical Infrastructure Supports Continuous Manufacturing Operations
In the manufacturing sector, reliable electrical infrastructure is crucial for maintaining uninterrupted operations. Downtime, whether due to power outages, equipment failure, or inefficient systems, can be costly and disruptive. A well-designed electrical system ensures that all machinery and processes receive consistent power, reducing the likelihood of interruptions and enabling a seamless production flow. Moreover, these systems provide the flexibility needed to adapt to changing production demands, allowing manufacturers to scale operations up or down as required.
Integrating with Industry 4.0: How Industry 4.0 Technologies Are Transforming Manufacturing Processes
The advent of Industry 4.0 has revolutionised manufacturing, introducing advanced technologies such as automation, artificial intelligence (AI), and the Internet of Things (IoT). These innovations rely heavily on robust electrical installations to function effectively. For example, IoT devices require a stable and reliable power supply to continuously monitor and collect data from manufacturing equipment. This data is then analysed using AI to predict maintenance needs, optimise production schedules, and reduce downtime
Automation, another key component of Industry 4.0, depends on precise and consistent electrical systems to operate machinery with minimal human intervention. By integrating these technologies into their electrical infrastructure, manufacturers can achieve greater efficiency, reduce errors, and enhance overall productivity.
Example Applications: Practical Examples of Electrical Installations in Various Manufacturing Settings
In practical terms, advanced electrical installations are applied across a wide range of manufacturing environments. For instance, in automotive manufacturing, smart control systems powered by reliable electrical infrastructure enable the automation of assembly lines, allowing for faster production with fewer errors. In food processing plants, IoT devices monitor environmental conditions such as temperature and humidity, ensuring that products are manufactured under optimal conditions to maintain quality and safety.
Additionally, in high-tech industries like electronics, advanced electrical systems support cleanroom environments where even minor power fluctuations could lead to significant defects in production. By investing in state-of-the-art electrical installations, manufacturers can safeguard their processes against such risks, ensuring consistent and high-quality output.
Key Components of Advanced Electrical Installations
Advanced electrical installations are composed of several key components that collectively enhance the efficiency, reliability, and sustainability of manufacturing processes. These components include smart control systems, predictive maintenance and IoT integration, data analytics for process optimisation, and energy management solutions. Each of these elements plays a vital role in modernising manufacturing operations and ensuring they meet the demands of today’s competitive market.
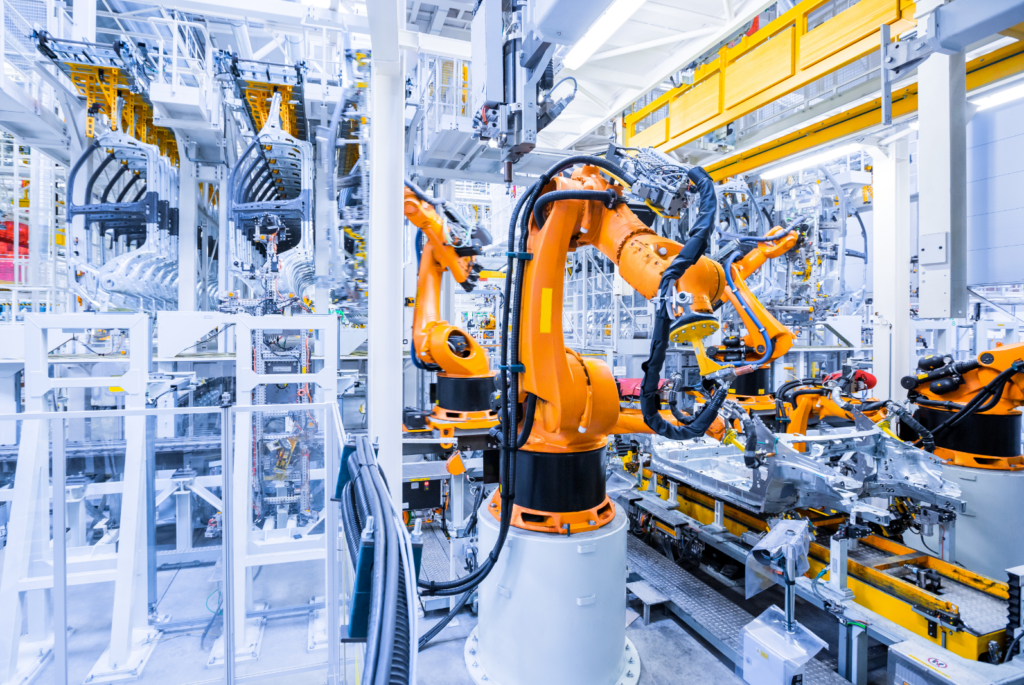
Smart Control Systems: Streamlining Operations and Reducing Human Error
Smart control systems are at the heart of automation in manufacturing. These systems, powered by advanced electrical infrastructure, allow for the precise control of machinery and processes with minimal human intervention. By automating repetitive and complex tasks, smart control systems reduce the likelihood of human error, improve consistency in production, and significantly increase operational efficiency
For example, in an automated assembly line, smart control systems can adjust machinery settings in real time based on the specific requirements of each product being manufactured. This level of precision not only enhances productivity but also ensures that products meet exacting quality standards.
Predictive Maintenance and IoT Integration: Minimising Downtime through Real-Time Monitoring
Predictive maintenance, enabled by IoT integration, is a transformative approach to equipment management. By using sensors to monitor the condition of machinery in real time, IoT devices collect data on factors such as temperature, vibration, and energy consumption. This data is then analysed to predict when maintenance is needed, allowing for timely interventions before a breakdown occurs
The integration of IoT with advanced electrical installations ensures that manufacturing equipment operates at peak efficiency, reducing unplanned downtime and extending the lifespan of critical assets. For instance, a sensor detecting unusual vibrations in a motor can trigger a maintenance alert, allowing technicians to address the issue before it leads to a complete shutdown. This proactive maintenance strategy is a key factor in maintaining continuous production and avoiding costly disruptions.
Data Analytics for Optimisation: Leveraging Big Data for Continuous Improvement
In today’s data-driven world, the ability to analyse vast amounts of information is crucial for optimising manufacturing processes. Advanced electrical installations equipped with data analytics capabilities allow manufacturers to collect and process data from various sources, including machinery performance metrics, production rates, and energy usage
By analysing this data, manufacturers can identify inefficiencies, predict potential issues, and implement improvements that enhance overall productivity. For example, data analytics can reveal patterns in energy consumption, helping to optimise the use of resources and reduce costs. Additionally, continuous monitoring and analysis enable manufacturers to adapt quickly to changing production demands, ensuring that operations remain efficient and responsive to market needs.
Energy Management Solutions: Reducing Costs and Environmental Impact
Energy management is a critical component of advanced electrical installations, particularly in an era where sustainability is increasingly important. Modern energy management solutions allow manufacturers to monitor and optimise their energy consumption, reducing both operational costs and environmental impact
These systems can automatically adjust energy usage based on real-time data, ensuring that only the necessary amount of power is used at any given time. For instance, during periods of low production, energy management systems can reduce power to non-essential equipment, thereby conserving energy and lowering costs. Moreover, by minimising waste and improving efficiency, these solutions contribute to a smaller carbon footprint, helping manufacturers meet regulatory requirements and align with global sustainability goals.
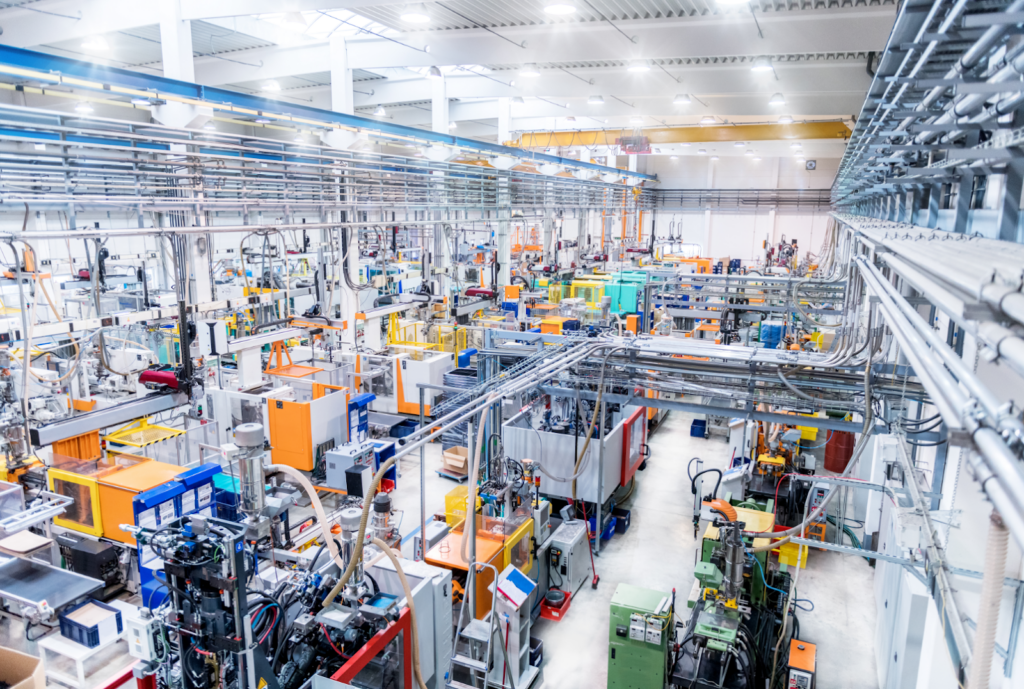
Benefits of Optimising Electrical Installations in Manufacturing
Optimising electrical installations in manufacturing is not just about upgrading systems—it’s about unlocking a range of benefits that can significantly improve operational efficiency, reduce costs, and enhance overall productivity. This section explores how such optimisations lead to increased productivity, cost reduction, enhanced flexibility, and a reduced environmental impact.
Increased Productivity: Achieving Smoother Operations with Fewer Interruptions
One of the most immediate benefits of optimising electrical installations is the substantial increase in productivity. By integrating advanced technologies like smart control systems and predictive maintenance, manufacturers can ensure that their equipment operates more efficiently and with fewer interruptions. For instance, the use of IoT devices for real-time monitoring enables quick responses to potential issues before they escalate into major disruptions, thereby maintaining a smooth and continuous production process
Moreover, automation systems driven by optimised electrical infrastructure can handle complex and repetitive tasks with greater accuracy and speed than human operators, further boosting productivity. This allows manufacturers to produce more in less time, meeting increasing market demands without compromising on quality.
Cost Reduction: Long-Term Savings through Optimised Systems
Cost reduction is another significant advantage of optimising electrical installations. By improving energy efficiency and reducing downtime, manufacturers can achieve substantial savings over the long term. Energy management systems, for example, can reduce energy consumption by ensuring that power is only used when and where it’s needed, cutting down on waste and lowering utility bills
Additionally, predictive maintenance strategies enabled by IoT integration help to avoid costly repairs and downtime by addressing issues before they lead to equipment failure. This proactive approach not only extends the lifespan of machinery but also reduces the need for emergency maintenance, which is often more expensive and disruptive than planned upkeep
Enhanced Flexibility: Adapting to New Technologies and Market Demands
Optimised electrical installations provide the flexibility needed to adapt to new technologies and changing market demands. As manufacturing processes evolve, so too do the requirements for electrical infrastructure. An optimised system can easily integrate new technologies such as AI, robotics, and advanced data analytics, allowing manufacturers to stay ahead of industry trends and respond swiftly to shifts in demand
For example, in a fast-paced manufacturing environment, the ability to quickly reconfigure production lines or scale operations up or down is crucial. Electrical systems that are designed with flexibility in mind can support these changes without requiring significant downtime or costly modifications, ensuring that manufacturers remain competitive and agile.
Sustainability and Environmental Impact: Contributing to a Greener Future
In today’s environmentally conscious world, reducing the carbon footprint is a key priority for many manufacturers. Optimising electrical installations plays a vital role in achieving this goal by improving energy efficiency and reducing waste. Energy management solutions, for instance, help manufacturers minimise their environmental impact by optimising power usage and reducing emissions
Furthermore, advanced electrical systems can support sustainable practices such as the integration of renewable energy sources, which not only contribute to a greener future but also offer long-term cost savings. By aligning their operations with global sustainability goals, manufacturers can enhance their corporate reputation and meet regulatory requirements more easily.
Conclusion
In today’s competitive manufacturing landscape, the role of advanced electrical installations is more critical than ever. From increasing productivity and reducing costs to enhancing flexibility and sustainability, optimised electrical systems are essential for manufacturers aiming to stay ahead of the curve. By leveraging the latest technologies and integrating them into a robust electrical infrastructure, manufacturers can ensure that their operations run smoothly and efficiently, positioning themselves for long-term success.
Power Your Manufacturing Future with Elite Electrical
Elite Electrical Contracting Ltd. brings over 20 years of expertise to ensure your manufacturing operations are not only efficient but future-ready. Whether you need a system upgrade or a brand-new installation, our team is committed to delivering tailored solutions that drive productivity and sustainability.
Let’s make your manufacturing processes smarter, faster, and greener—starting today.
Contact Us:
- Address: 30 Upper Mulgrave Road, Sutton, Surrey, SM2 7BD
- Phone: 020 8644 3200
- Email: [email protected]